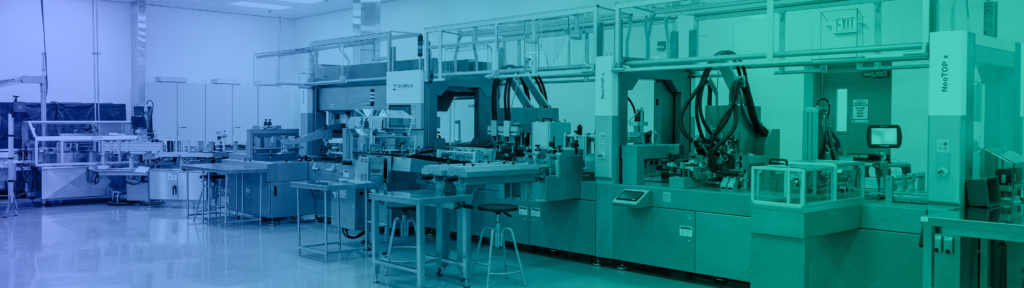
When developing a sterile product, people often do not understand what’s required to manufacture the product. Does the molecule require aseptic filling, or can it be terminally sterilized? Is the application truly a sterile program and how do they find the right CDMO to manufacture their product safely and effectively? Below we will review the differences of common sterile fill/finish approaches, what dosage forms typically require this level of production, and how Renaissance can facilitate your sterile fill/finish needs.
What is Aseptic Fill Finish?
Aseptic fill finish is a process that fills drug product into its final primary packaging absent of microorganisms and pyrogens. During this single process, sterility is maintained from filling to packaging. To achieve this, packaging components are introduced to an aseptic filling line pre-sterilized, or components are sterilized in line prior to filling. Bulk drug product is filtered through a 0.22 micron filter to remove any potential contaminates prior to entering the filling equipment. The filling processes then takes place in a ISO5/Class A area to allow sterilized packaging components and drug product remain sterile throughout the process.
What is Terminal Sterilization?
Terminal sterilization is the process of sterilizing product in its primary packaging using heat or radiation. First, the API and excipients of a formulation are compounded and filled into vials (or other primary packaging container) and stoppered. The assembled product is then subjected to high heat or radiation for a period of time until the product is sterilized. Terminal sterilization is the FDA’s preferred method for manufacturing sterile products however many drug products cannot withstand the harsh conditions of the process without degrading or impacting product efficacy. For products requiring sterility, that cannot withstand terminal sterilization, aseptic manufacturing is required.
What is the difference between Terminal Sterilization and Aseptic Processing?
In contrast to an aseptic fill finish process, terminal sterilization occurs after the drug product has already been manufactured and packaged. During an aseptic fill finish process, packaging components and the drug product are sterilized prior to being combined under sterile conditions.
Why is Aseptic Fill Finish required?
Aseptic fill finish is required because many drug products cannot be sterilized after filling due to sensitivity to heat, radiation and other terminal sterilization methods which may impact product effectiveness. The only way to manufacture a sterile product without terminal sterilization, is to use an aseptic fill finish process that maintains sterility from beginning to end.
What are the types of drug products that require Aseptic Fill Finish?
Many drug products that require aseptic fill finish are liquids prepared in a solution or a suspension, including the following:
- Injectable drugs (small volume parenteral)
- Preservative-free nasal sprays
- Subcutaneous Injections
- Implantable drugs
- Ophthalmic Products
- Lyophilized (freeze-dried) powders meant to be re-suspended at final use
What are the challenges associated with Aseptic Fill Finish?
The aseptic fill finish process is a complex interaction between the drug product, equipment, personnel, and the facility. As a result, maintaining sterility inside a clean room can be challenging. Manufacturing equipment and each packaging component must be individually sterilized prior to filling. Room monitoring must be performed throughout the manufacturing process to ensure that proper conditions are maintained. Personnel must be highly skilled, effectively trained, and experienced. Finally, specialized equipment must be qualified and validated for each product manufactured. In addition, the processes are challenged on a regular basis with media fills which fill the containers with a growth promoting media to ensure that the process continues to be in control.
Equipment
To fill product aseptically it requires specialized equipment that can maintain ISO 5/Class A conditions within the filler/room. This equipment must be placed in a manufacturing space that has a progression for personnel and materials that begins in ISO 7/Class C, transitions to ISO 6/ class B to the filling equipment or suite. Modern aseptic filling equipment utilize RABS (restricted access barrier system) or isolator technology. Both RABS and Isolators restrict outside contamination during the filling process and maintain ISO 5/Class A conditions inside the filling and packaging areas. These rooms are more commonly referred to as clean rooms.
What is a Clean Room?
A clean room is a room that is environmentally monitored for air quality, particulate matter, temperature, humidity, air pressure and microbial contamination to ensure that the space meets all the sanitary requirements to manufacture products under cGMP conditions. Depending on the product being produced, clean rooms can have different levels of classification. For aseptic manufacturing, product must be filled under the most stringent conditions of ISO 5/Class A (Class 100) room standards. In a clean room, drug product, filling equipment, and personnel are all monitored for particulate and micro burden and when combined need to meet the particulate standards of each clean room area. Personnel working in a clean room are highly trained in aseptic process to safely handle material and equipment to ensure product is effectively manufactured to meet the sterility of the drug product. The goal of a clean room is to successfully filter out any microbiological or particulate contamination using special air filters. In addition, all surfaces inside the clean room are frequently and routinely deep cleaned to prevent the growth of microbes. Even the gloves, clothes, and other PPE (personal protective equipment) used by the clean room personnel undergo special cleaning procedures to maintain sterility once inside the room.
The Renaissance Approach
At Renaissance, our team has designed dedicated parts of our facility to readily handle your most challenging aseptic fill finish needs. We have invested in state-of-the-art equipment and processing areas to ensure your drug product is manufactured under the strictest quality standards. We manufacture our own water for injection (WFI) on site and generate clean steam using WFI to support our cleaning processes as well as product heating, if required. Renaissance offers dedicated manufacturing suites to compound bulk drug product which feeds into two aseptic filling suites. These suites contain lines capable of filling injectable products in vials/stoppers and preservative-free nasal sprays (vial/snap-on nasal pumps). Our filling lines utilize RABS technology and are validated to support a wide range of packaging components. Each line can facilitate either aseptic sterile processing or terminal sterilization and both lines are currently manufacturing FDA approved commercial products, in addition to numerous development programs at the clinical trial level.
Conclusion
Renaissance has decades of experience in development and filling of aseptic products at the highest level for the US and global markets. Located on the east coast of the United States, our state-of-the-art facilities and equipment can support a broad range of sterile and/or environmentally controlled products. We offer a full spectrum of sterile services capabilities including small molecule and biologic fill capabilities, controlled substances (DEA Schedule I-V), and potent compounds (through SafeBridge 3). Our experienced teams can also provide support on formulation development, method validations, analytical testing, and more.
From early-stage development through commercial production, Renaissance offers the expertise and regulatory track record to make us the perfect partner for your sterile injectable and preservative-free nasal spray programs. For more information please visit www.renpharm.com