Overview: The following case study is a collaboration with Renaissance Lakewood and Raven consulting on continuous improvement of Renaissances manufacturing processes. The study outlines the previous operational challenges and how Raven’s digital OEE software was integrated into Renaissance’s manufacturing processes to drive continuous improvement.
The Challenge
When walking production lines, Renaissance management teams saw basic whiteboards and data capture systems being used to track production information — but they didn’t always reflect what was actually happening on the shop floor. Additionally, the data wasn’t being used for historical reference or root cause problem-solving. At the end of the day, a supervisor would take a photo of the whiteboards, and the information was erased. Operators weren’t always motivated to fill out the information since they felt it didn’t provide them value or even understand why they had to do it.
To build a sustainable continuous improvement strategy, Renaissance was looking for a digital OEE improvement solution that accelerated continuous improvement in their factory through operator engagement and frontline discussions. The solution that could effectively democratize their data would also streamline their process of collecting and sharing production data and enhance visibility. In order for the factory to work more efficiently, the OEE software chosen needed to help their team:
- Engage the frontline operators and figure out how their day was really going
- Have two-way, data-driven conversations to resolve real-time and systemic issues across the plant
- Collect operator context to understand the root cause of production losses and downtime
- Develop successful continuous improvement initiatives to achieve stronger results
The Solution
Renaissance implemented Raven’s OEE improvement software and started using it to resolve challenges with data democratization. Their aim was to help build trust and collaboration among frontline and operations teams, and make sure that their workers knew their production insights were valuable. Renaissance started off by piloting Raven on one of their packaging lines and were able to:
- Use whiteboards to facilitate team interactions instead of just capturing machine data, and empower operators to tag downtime and provide important context about what was happening on their line with the touch of a button
- Account for 100% of production time, real-time visibility, and historical reporting, to initiate fact-driven conversations with operators and management
- Give operators and supervisors data that mattered to them at their fingertips, where they determined there was start time variability and identified opportunities for improvement
- Drive maintenance practices, improve their preventive maintenance practices, and work on condition monitoring
- Set up end-of-line dashboards so the frontline could see how their work impacts their start time goals and brings meaning to their day-to-day responsibilities
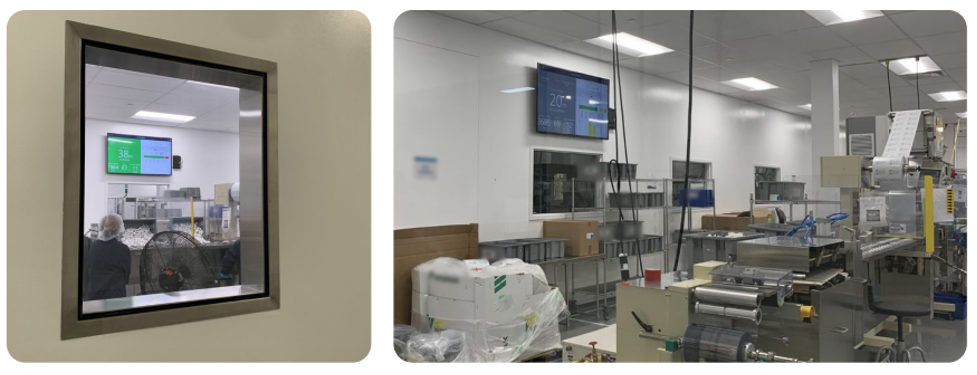
The Results
The frontline team was excited to report record-setting performance on their filling and packaging lines. It was a direct result of day in and day out engagement by the operators, the engineers, mechanics, and other contributing teams.
Over time, Renaissance has increased their downtime tagging rate and data is now more meaningful and accurate, allowing their teams to make data-led productivity improvements. Some examples of how their data was used to support their continuous improvement initiatives are:
- Flagging opportunities to prevent future production issues, by recognizing shifts in the downtime bottleneck
- Using Raven’s contextualized timeline to drive maintenance schedules, improve preventive maintenance practices and condition monitoring
- Communicating results with clients that use Raven on their lines. The Renaissance management team was thrilled by how responsive their clients were to the production data available. Without having to “gown up”, they can talk them through production in real-time.
Renaissance’s top 3 CI priorities moving forward include:
- Initiating more frontline training to help operators recognize their problem-solving capabilities
- Expanding the installation of Raven across the rest of their site
- Having more frequent data-led conversations both internally and externally
About Raven
Raven is a manufacturing technology leader that helps companies empower the frontline and improve operational performance with our automated contextualization and OEE software. Raven combines and analyzes data from machines and input from operators to provide a real-time, meaningful timeline of events with context for everything that’s happening on the line — accounting for 100% of production time and losses.
Learn more at www.raven.ai
About Renaissance Lakewood
Renaissance Lakewood, LLC is a US-based contract development and manufacturing organization for pharmaceutical and biotech companies. Located in Lakewood, New Jersey, Renaissance’s 370,0000+ square foot facility has 10+ cGMP manufacturing suites, with additional suites under construction. With over 20+ years of experience, Renaissance has a proven track record of moving customers from R&D to commercial launch in nasal sprays and sterile injectable dosage forms. They’re also the first manufacturer of an FDA approved bi-dose nasal spray drug. As a purpose-driven team, Renaissance takes pride in producing safe, reliable, life-saving medicines on behalf of their customers and patients